The digital revolution in the industrial sector is driven by the proliferation of sensors and is transforming the way industries operate in terms of process monitoring and data usage. Sensors implemented in each of the process nodes continuously collect vast amounts of data creating a dynamic stream of information crucial for various applications. By harnessing the power of real-time data collection and advanced analytics, sensors play a critical role in process optimization thereby enhancing overall efficiency and productivity.
As technology advances, the role of sensors in orchestrating the future of industrial operations will become increasingly pivotal. The continuous evolution of sensor technology promises to enhance the precision, efficiency, and intelligence of industrial systems, further driving innovation and productivity across various sectors. In today’s connected world, the efficient processing and management of data are paramount for the success of businesses. With an exponential growth in data generation propelled by the increasing number of sensors implemented at different process nodes and Industrial Internet of Things (IIoT) enabled devices, there is an unprecedented demand for advanced data processing and management strategies within industrial environments.
Key characteristics of IIoT
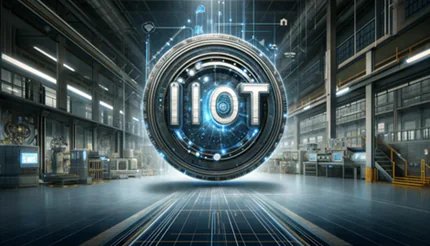
- Industrial focus: IIoT is designed for industries and sectors where operational efficiency and safety are paramount, including manufacturing, energy, healthcare, and agriculture.
- Data collection: IIoT entails gathering extensive data from sensors, devices, and equipment within industrial environments.
- Real-time analytics: IIoT platforms utilize real-time analytics to process and analyze data, offering insights for optimizing operations.
- Predictive maintenance: A significant application of IIoT is predictive maintenance, where data is leveraged to forecast when industrial equipment requires servicing, thereby minimizing downtime and reducing costs.
- Integration with existing systems: IIoT solutions are often required to integrate with existing industrial control systems and legacy equipment.
The sensor symphony in action
The global industrial sensors market is forecasted to experience significant growth of CAGR of 9% between 2022 and 2027. The market’s growth is driven by several key factors, such as the rising demand for intelligent manufacturing systems, the miniaturization of sensors, and the increasing adoption of wireless monitoring technologies. With advancements in sensor technology and the proliferation of Industry 4.0 initiatives, the market is poised for sustained expansion, catering to the evolving needs of modern industries striving for efficiency and competitiveness in the global landscape.
Nutanix, Inc., a US-based cloud-computing company, provides intelligent, scalable hybrid-cloud solutions tailored for enterprises and industries to manage their rapidly expanding unstructured data and avoid data overload. Nutanix Files and Nutanix Objects offer the flexibility and control needed for comprehensive data storage and management by supporting VM, file, block, and object storage on a single platform.
The global industrial data analytics market size is expected to grow at a robust CAGR of 13.84% between 2023 and 2027. This growth is driven by advanced data processing techniques that analyze sensor data using sophisticated algorithms. These algorithms identify patterns, predict equipment failures, and optimize production lines, thereby unlocking significant value in the data analytics market. The core of the data analytics revolution lies in its ability to process vast amounts of data generated by interconnected sensors and devices.
The glitches in the symphony: Teething challenges
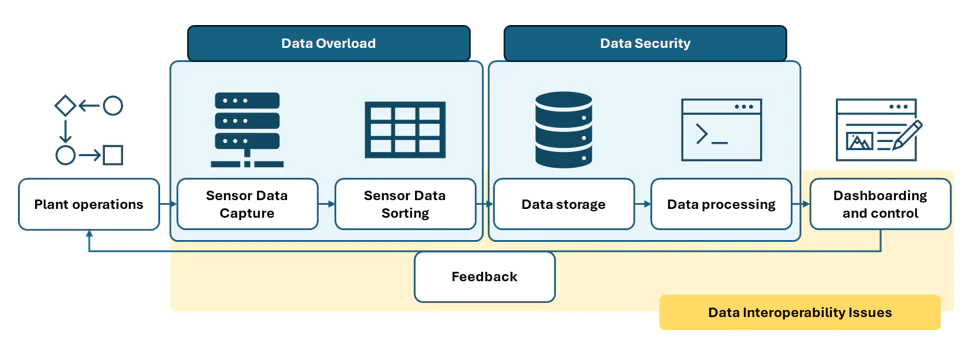
Industrial operation is composed of diverse processes; to monitor the complete process, different checkpoints need to be placed. Sensors and mission vision are the technologies, which are widely implemented for data collection, monitoring, and sending signals to field devices for control. With a clear directive in the overall process, sensors continuously capture the field information and pass the same to local or central data management systems, which act as the control systems in the industrial sector.
Data overload
Continuous monitoring and data captured from the sensors play a pivotal role in overall process control and management. The detailed data captured through the industrial sensors also provide some amount of junk information, which will be rejected by the control system after a set of redundant process steps. This redundancy will cause a delay in the data processing of ideal sensor information. This scenario is currently pitched with the implementation of AI and ML in the data capturing and storage process. The control platform enabled with AI and ML capabilities directs the sensors to reject unwanted information at the source and processes only relevant information from the field devices.
Data security
With increased connectivity brought about by the proliferation of IIoT devices in industrial settings, data security has become increasingly critical. The interconnected nature of these devices and the continuous exchange of data create a larger attack surface, increasing the potential vulnerability to cyber threats.
Cisco Cyber Vision streamlines the deployment process, even on a large scale, by offering a comprehensive view of industrial operational technology (OT) security posture. It is designed for seamless integration into industrial network infrastructure, providing clear visibility of all the industrial assets and their communication patterns. It spotlights devices that need immediate attention and suggests solutions.
Lack of data interoperability
Industrial systems often involve a hodgepodge of sensors from different vendors, each with its own communication protocols and data formats. Different vendors often use proprietary communication protocols (such as Modbus, Profibus, and DeviceNet) for their sensors and equipment. These protocols may not be compatible with each other, requiring custom solutions or middleware to translate data between them.
Reltio, a US-based software company, offers Reltio Connected Data Platform, an AI-powered, cloud-native SaaS Master Data Management (MDM) platform for interoperable data. Addressing the lack of data interoperability requires a strategic approach involving standardization, middleware solutions, and possibly advocating for industry-wide adoption of open standards. By overcoming these challenges, industrial enterprises can unlock the full potential of their data, enabling more efficient operations and informed decision-making.
The harmony of solutions: New technologies
Edge computing
By processing data at the edge, only relevant data or summarized results are transmitted to centralized systems or the cloud. This reduces the amount of raw data that needs to be sent over the network, thereby optimizing bandwidth usage and reducing operational costs associated with data transmission. Edge computing significantly reduces latency and enhances reliability by reducing dependency on a centralized data center or cloud infrastructure.
KORSCH AG, a leading global specialist in manufacturing tableting systems, relied on Industrial Edge computing from Siemens. The advantage of this Industrial Edge is that all sensors and IoT devices can be centrally managed across all machines, process lines, and production facilities. This creates powerful scaling effects and saves time, human resources, and costs in the productive rollout of edge computing applications.
Quality control is pivotal in manufacturing due to the potential consequences of defective products, including customer dissatisfaction, recalls, and financial setbacks. Edge computing enhances quality control processes by enabling real-time analysis of production data. Embedded sensors in machinery or production lines continuously capture live data on parameters like temperature, pressure, and humidity. Edge devices, equipped with sophisticated analytics algorithms, can instantly analyze this data on-site, comparing it against predefined standards and issuing alerts for any deviations. This capability allows manufacturers to promptly implement corrective actions, thereby maintaining superior product quality and reducing the incidence of defective products reaching consumers.
Bosch and ExxonMobil are collaborating to explore the application of blockchain technology for secure data exchange in the oil and gas industry. This partnership aims to leverage blockchain’s capabilities to enhance the security, transparency, and efficiency of data transactions and communications within the industry.
Blockchain technology
Blockchain technology revolutionizes secure data exchange by offering decentralized, immutable, transparent, and secure mechanisms for recording and verifying transactions. Its adoption continues to grow as organizations seek reliable solutions to enhance data security and streamline operations. Unlike traditional centralized systems where data is stored in a single location, blockchain distributes data across a network of computers (nodes). Each node maintains a copy of the entire blockchain ledger, ensuring redundancy and reducing the risk of a single point of failure.
The future symphony: Emerging trends
Several promising trends are poised to further revolutionize industrial sensor data processing and management:
Sensor fusion
This technology combines data from multiple sensors to create a more comprehensive picture of a system’s health. By fusing data from multiple sensors, the technology can compensate for individual sensor limitations or biases. It provides a more accurate and reliable assessment of the system’s performance, environmental conditions, or user activity. It plays a crucial role in enabling smarter, safer, and more efficient applications in autonomous vehicles, healthcare, aerospace, industrial IoT, and beyond.
Qualcomm has introduced the new Qualcomm Aware Platform (Qualcomm Aware), aimed at digitally transforming value chains across various global industries. This platform, powered by IoT-optimized silicon, provides a robust foundation for building integrated, power-efficient solutions. Equipped with sensor fusion capabilities, Qualcomm Aware offers contextual insights by measuring changes in temperature, light, humidity, pressure, and other variables based on specific use cases. Its edge-to-cloud processing and communication ensure a secure, low-latency, and power-efficient solution, adaptable to any device design.
Scalable IoT platforms
The development of scalable IoT platforms is crucial for managing the growing volume and diversity of sensor data in industrial environments. These platforms must offer robust capabilities for data management, storage, and processing to ensure efficient and effective operations.
Software AG’s Cumulocity IoT platform is an IoT platform that handles data logging, storing, and processing from many devices and locations in industrial environments. It can orchestrate action based on real-time data, and coordinate the long-term storage and analysis of large data sets to power analytics. It delivers enterprise-grade IoT with unrivaled reliability, security, and performance.
Conclusion
The industrial sensor symphony is a complex and ever-evolving soundscape, composed of a myriad of data streams from diverse sensors that monitor and measure various aspects of industrial operations. This dynamic environment requires continuous adaptation and innovation to manage effectively. By tackling these challenges and adopting cutting-edge technologies, industries can convert the chaos of raw sensor data into a well-orchestrated symphony of operational efficiency and productivity. This harmonious integration of data and technology leads to enhanced efficiency, improved productivity, and ultimately, a more competitive and resilient industrial landscape.